Ultrasonic soldering/metalisation/plating/tinning Principle and procedure
S-Bond® ultrasonic soldering is a material-to-material joining process with filler material. High-strength metallurgical joints are created by the action of heat and sound waves with a high energy density. Even materials that are difficult to wet, such as light metals, ceramics, composites and glasses, can be wetted and brazed by the ultrasonic brazing process at brazing temperatures from 100 °C without flux. The solders used are lead-free and comply with the RoHs guidelines.
Ultrasonic soldering is particularly suitable for:
- Gas-tight and suitable for low-temperature/vacuum applications
- Flat and localised metalising (spot metalisation and spot repair)
- High heat resistance with very good electrical and thermal conductive metallic material transitions
- Thermal shock resistant
- High shear strength due to metallurgical bonding
- Thermal stress-free brazing even with materials of different thermal expansion coefficients
- High corrosion resistance of solder joints due to flux-free process control
- Large selection of solder materials for optimum process design
- Patented, lead-free solder materials can be used in accordance with RoHS directives
- Flux-free and stable joining in the range from 100°C to 450°C, even for thermally sensitive materials and geometries
- Process control in atmosphere, under inert gas and vacuum
Atmospheric soldering is usually performed with aggressive fluxes to remove or break up oxidised surfaces and remove impurities. Furthermore, especially at low process temperatures, it is difficult to directly solder materials such as glass or ceramics without metallisation. By using ultrasonic energy, the use of fluxes can be dispensed with. While the solder is still liquid, the ultrasonic effect creates cavitations that cause compressive stress peaks. This cleans the surfaces to be wetted and breaks up oxide skins. The liquid solder can thus wet the surface. In addition, trapped gases are removed from the liquid solder joint by the high-frequency excitation. This results in void-free and clean solder joints. Soldering with ultrasound does not cause any corrosion of the solder joints. There is no need for time-consuming cleaning and removal of flux residues. The solder joints are mechanically stable, gas-tight, very good heat conductors and suitable for vacuum. Also particularly suitable for contacting on the thinnest of metallisations as well as pre-brazing materials that are difficult to wet such as light metals, composites, glasses and ceramics.
Ultrasonic soldering and metalisation of ceramics
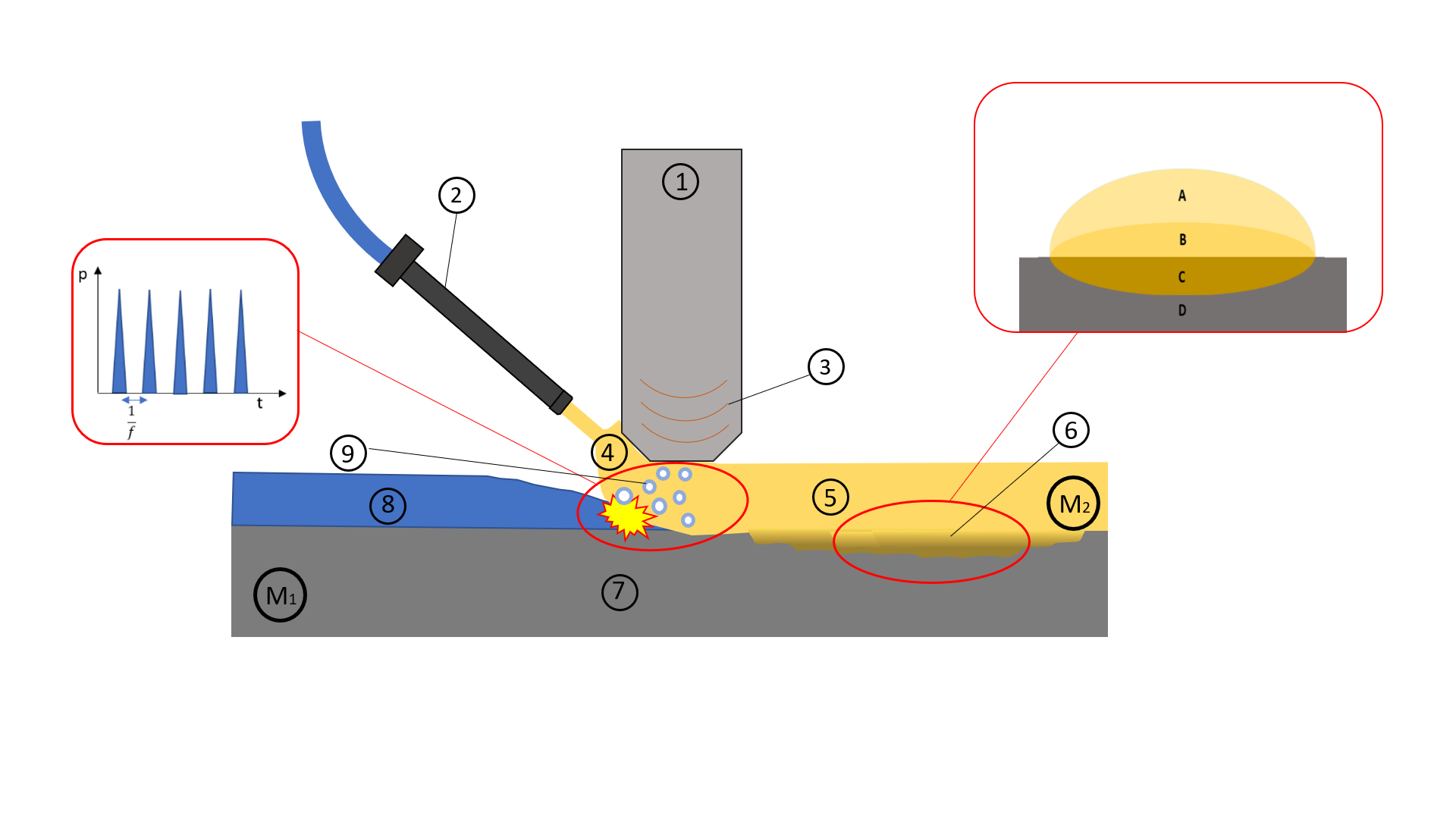
Legend
- Sonotrode(heated)
- Solder feed
- Ultrasonic(axial)
- Solder-liquid
- Solder-solid
- Diffusionszone(B,C)
- Metal
- Oxid layer
- Cavitation
- Solder
- Diffusion zone in solder – excess of solder alloy elements
- Diffusion zone in the base material
- Base material
Legend
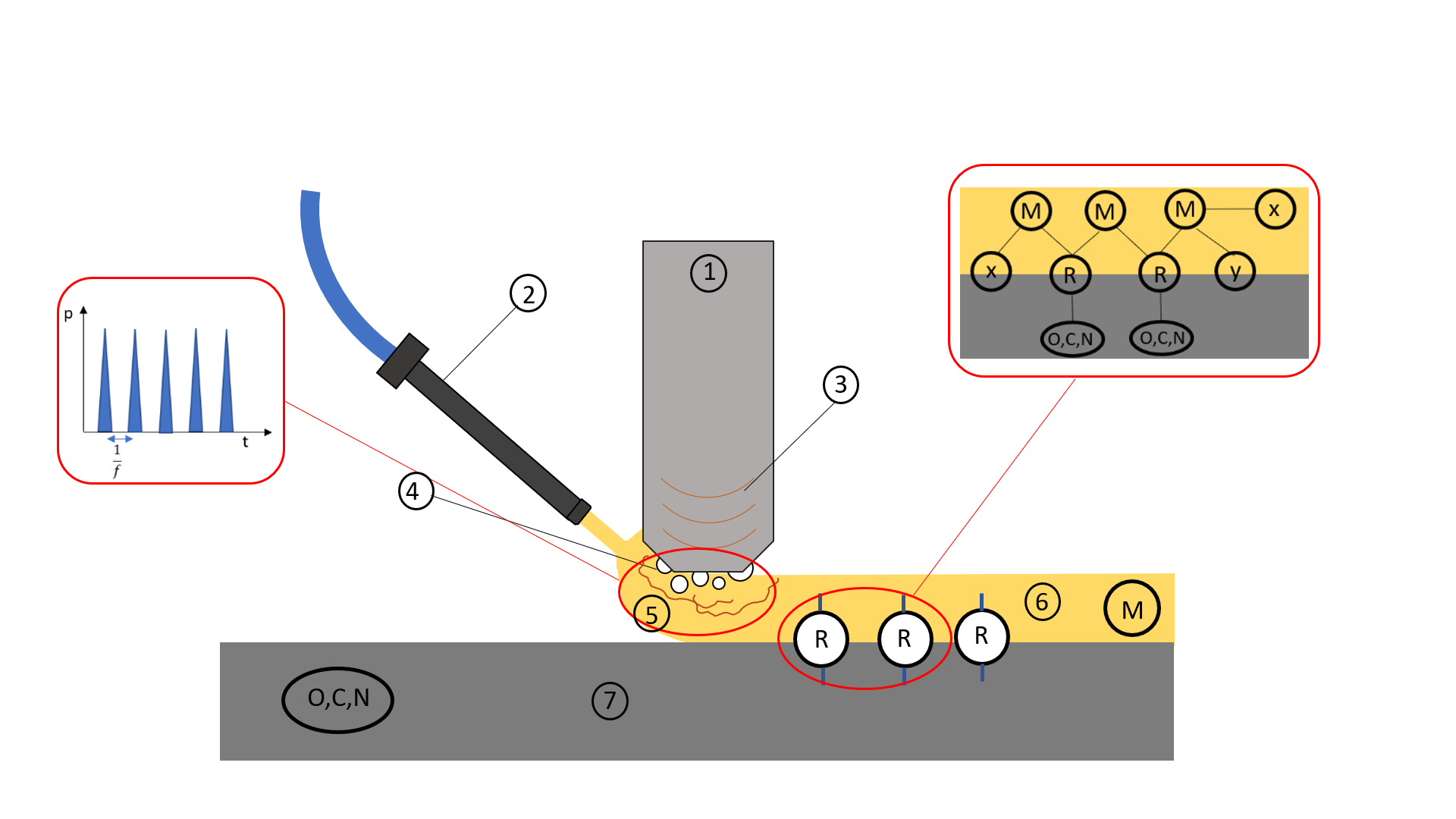
Ultrasonic soldering and metalisation of metals
- Sonotrode(heated)
- Solder feed
- Ultrasonic(axial)
- Cavitation
- Solder-liquid
- Solder-solid
- Ceramic/glas
Example ultrasonic soldered joinings
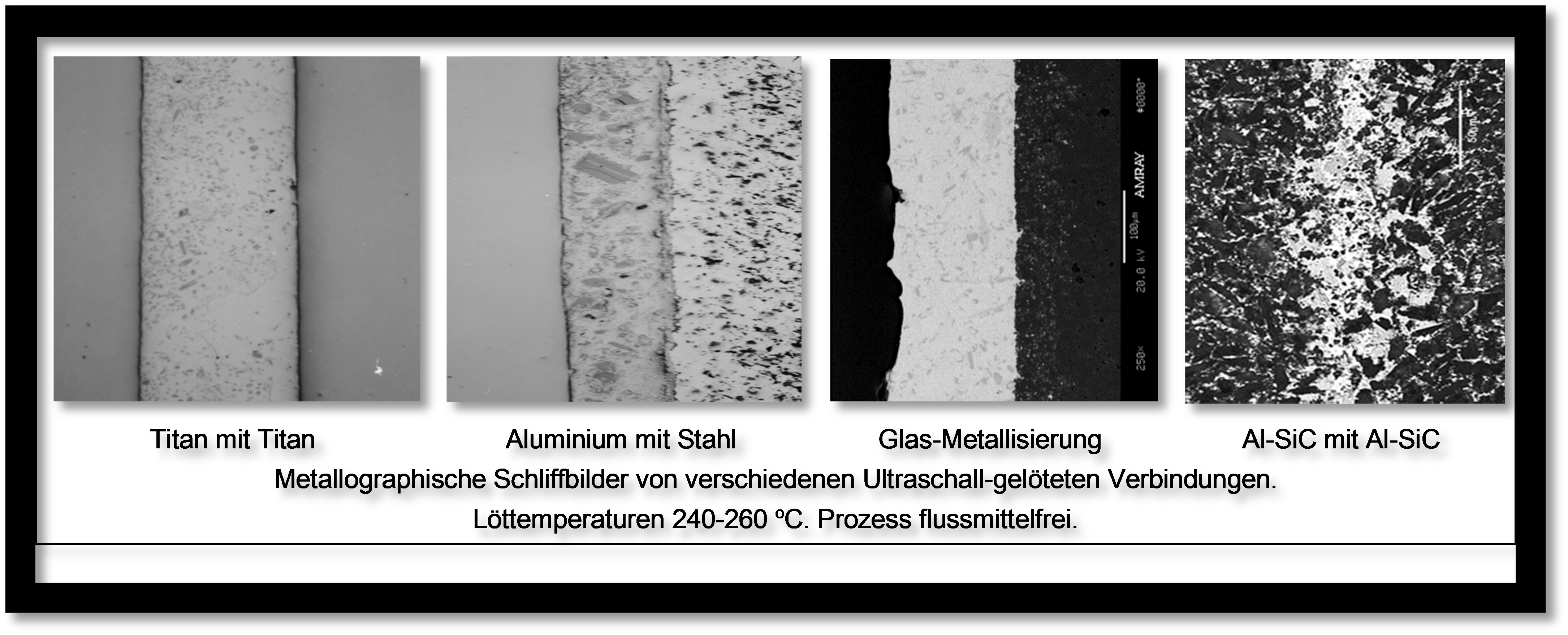